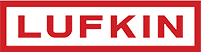
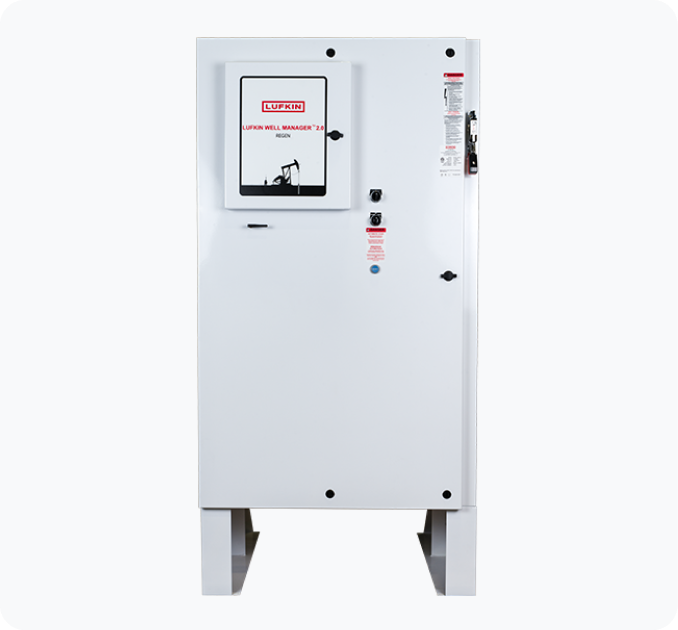
Well Control to Maximize Production
Oil wells require optimal pump operation, the LUFKIN Well Manager™ 2.0 Variable Speed Drive (LWM 2.0 VSD) integrates next generation pump-off control with variable speed control for optimum productivity for every stroke. Fully integrated LWM 2.0 VSD technology provides immediate and accurate downhole information, enabling the controller to match pump displacement to the well’s inflow in realtime.
Features
- Programmable and automated intra-stroke speed changes on the fly based on live surface or down hole dynagraph data
- Controller and VSD Setup, initialization and control with a single user interface
- Compatible with most available SCADA systems
Maximize Asset Value, Minimize Operating Expense
The Variable Speed Drive (VSD) protects equipment by adjusting pump speed as well conditions change to minimize fluid pound conditions, avoid working load violations and motor overload. The LUFKIN Well Manager (LWM) 2.0 monitors all aspects of production, such as pump fillage, motor torque and pumping unit balance conditions. The LWM 2.0 is serially integrated with the VSD and is capable to reset a VSD trip condition and automatically restart the system when deemed safe.
Customized to Well Conditions
The VSD cabinet arrives to location fully assembled, integrated with the LWM 2.0. Operators with limited experience will find the Quick Start programming function intuitive to operate, setup and edit the default parameters that are appropriate for most well conditions. For conditions that require advanced precise control, settings can be finetuned using the local color LCD user interface or via a remote SCADA interface connection. Additionally, an operator may connect with a laptop computer, tablet PC or mobile smart device, utilizing the local Wi-Fi connection.
The VSD system stays in tune with a well’s production by constantly monitoring well conditions and adjusting pump speed based on dynamometer card readings. The system is capable of mitigating undesirable operating conditions such as gas interference, rod float, fluid pound and pump tagging.
6-pulse VSDs are available with Passive Harmonic Filters, installed inside the cabinet to mitigate harmonic distortion. Harmonic Filters are designed to meet the IEEE 519-2014 standard.
The VSD system stays in tune with a well’s production by constantly monitoring well conditions and adjusting pump speed based on dynamometer card readings. The system is capable of mitigating undesirable operating conditions such as gas interference, rod float, fluid pound and pump tagging.
6-pulse VSDs are available with Passive Harmonic Filters, installed inside the cabinet to mitigate harmonic distortion. Harmonic Filters are designed to meet the IEEE 519-2014 standard.
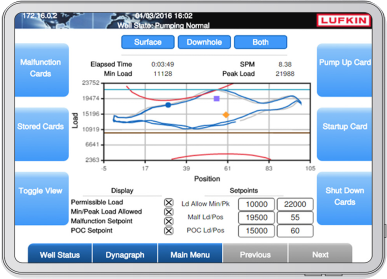
VSD Control Function
Intuitive dynagraph setup with permissible loads
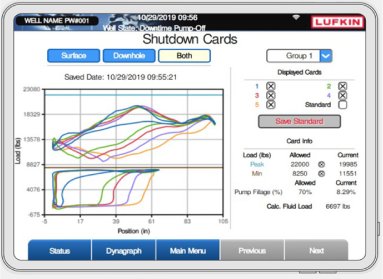
Shutdown cards
Multiple 5-card shutdown buffers, critical for diagnostics and Root Cause Analysis (RCA)
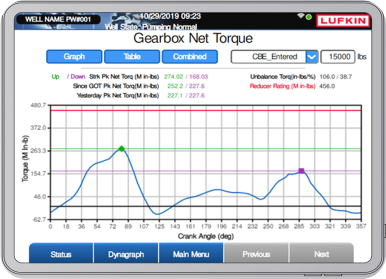
Gear Reducer Torque
For every stroke, the LWM 2.0 calculates gear reducer torque per 15 deg. Crank Angle intervals utilizing actual Polished Rod Load utilizing the API RP11E method. A VFD is not required to generate the torque plots!